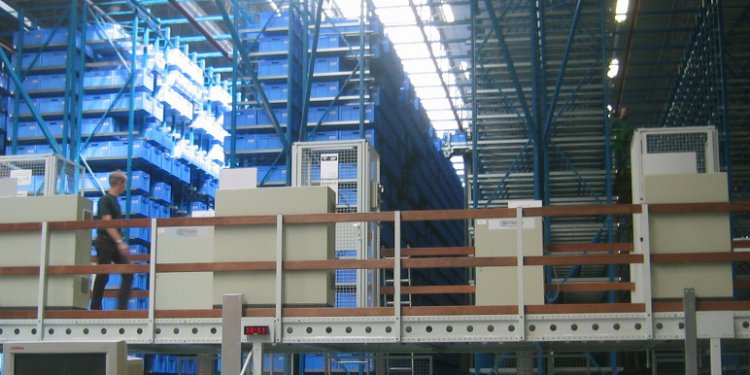
Materials Handling Magazine
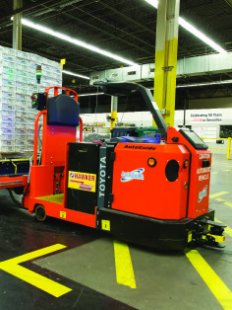
Global manufacturers that want to remain competitive are under constant pressure to reduce operating costs, become more efficient and get more than ever out of their existing facilities. Even lean operations must look for ways to drive continuous improvement and get leaner.
That was certainly the case when LEDVANCE, the manufacturer of traditional and LED lighting products formerly known as OSRAM SYLVANIA, decided to install automatic guided vehicles (AutoGuide) and specially designed, conveyor-topped carts in its 800, 000-square-foot facility in Versailles, Ky. The automatic guided vehicles (AGVs) are used in place of lift trucks to move empty pallets to the packaging line and palletized finished goods to a storage area. Loading and unloading pallets has also been automated.
“As we look to stay viable and sustainable, we need to be as competitive as we can, ” says plant manager Mike McNulty. “When we looked at where we were incurring costs, we found that we had some fork truck drivers who were doing little more than making a milk run, which was not the most value-added activity for those drivers.”
The result, says McNulty, is that four fork truck driver positions have been re-assigned to more meaningful work within the plant while congestion on the facility floor has been reduced. In addition, LEDVANCE is saving about $8, 000 a year in maintenance on fork trucks that are no longer needed and has seen a reduction in product damage due to driver error. “The project will earn a return on investment in just two years, ” says McNulty.
Choosing AGVs
LEDVANCE is a world leader in innovative lighting products as well as intelligent and connected lighting solutions for the smart home for consumers and professionals alike. The new company began to operate as a stand-alone subsidiary last summer, still going to market under the SYLVANIA brand in the United States and Canada.
The company has been producing lighting products at the Kentucky plant since 1964, and today it produces an estimated 500, 000 lamps per day. A highly automated facility, McNulty says the overall lighting industry has gone through a great deal of transformation over the last five years. “There has been a great deal of emphasis on energy savings and a shift to new technologies, like LED products that are greener for the environment, ” he says. “We have to produce products that meet those needs.”
As a global industry, there is excess manufacturing in the marketplace, which puts pressure on plants to be as efficient as possible to remain viable, sustainable and competitive. To that end, McNulty’s plant undertakes an annual “hoshin kanri” event, defined as a “comprehensive step-by-step planning process that takes a systems approach to change toward continuous improvement.”
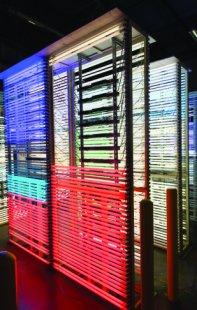
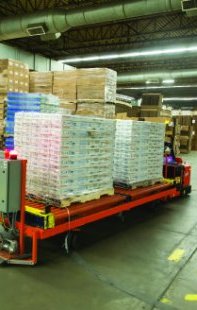